Labor Produktentwicklung
Hier finden Sie alle Informationen zu den Laboren Produktentwicklung des Fachbereichs Wirtschaftsingenieurwesen an der Hochschule in Weiden.
Ausstattung
- Stereolithographie
- FDM
- Vakkuumgießanlage
- 3D-Scanning
- Computertomographie
Der Markterfolg eines neuen Produktes wird bereits in den frühen Phasen der Produktentwicklung – insbesondere durch innovative Methoden und Werkzeuge – vorbestimmt. Ausgangspunkte sind dabei u. a. die 3D-Produktmodellierung und Simulation mit den entsprechenden CAx-Werkzeugen in Verbindung mit einem integrierten Wissens- und Informationsmanagement.
Um diese hoch gesteckten Ziele zu erreichen, bedarf es ausgewählter Strategien in der Konstruktion und Produktentwicklung. Eine durchgängige Produktentwicklung ist der entscheidende Schlüssel zu mehr Wettbewerbsfähigkeit. Durch die Implementierung der passenden Hard- und Softwarewerkzeuge im Unternehmen lassen sich die Entwicklungszyklen wesentlich straffen und die Produktivität erhöhen.
In Rahmen von Forschungs- und Entwicklungsprojekten stehen an der FH Amberg-Weiden folgende Laborausstattungen zur Verfügung.
Ausstattungsdetails
SL 250/50 - 3D Systems:
- Bauvolumen 250mm x 250mm x 250mm
- Datenaufbereitung Lightyear1.10
- Schnittstellen IGES, VDA, STL, Step, SAT
- Material Epoxyharze, Acrylate

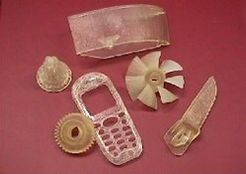

Stereolithographie
Prinzip:
Die bewegliche Basisplattform befindet sich in einer Prozesskammer, die flüssigem Kunststoff gefüllt ist. Für den Aufbau der ersten Schicht wird die Plattform bis knapp unter die Oberfläche gefahren. Ein Laser zeichnet die Konturen der ersten Schicht auf der Flüssigkeit nach. Durch die Lasereinwirkung härtet die Schicht an den gewünschten Stellen aus (Photopolymerisation). Die Plattform wird abgesenkt ein Schieber befördert neuen Kunststoff auf das Bauteil.
Werkstoffe: Epoxyharze und Acrylate
FDM
Stratasys FDM 3000:
- Bauvolumen 250mm x 250mm x 400 mm
- Datenaufbereitung QuickSlice V6.6
- Schnittstellen IGES, VDA, STL, Step, SAT
- Material ABS, Wachs, Polyamid, Elastomere




Fused Deposition Modelling (FDM)
Beim FDM-Verfahren wird das mit Hilfe von CAD (Computer Aided Design) konstruierte Bauteil mit einer speziellen Software in dünne Schichten zerlegt. Anschließend wird das Bauteil schichtweise aus Kunststoff aufgebaut – analog einem dreidimensionalen Drucker. Dabei wird ein auf einer Spule aufgewickelter Kunststoffdraht einem beheizten Extrusionskopf zugeführt und darin aufgeschmolzen. Das erwärmte Material wird dann durch eine feine Düse gepreßt und schichtweise aufgetragen, da sich der Kopf in x-y-Richtung bewegt und an den gewünschten Stellen Material auf der Grundplatte hinterläßt. Die Grundplatte senkt sich anschließend um einen kleinen Betrag. Der Kopf erzeugt nun eine zweite Schicht, welche die erste Schicht anschmilzt. Eine Vielzahl der Schichten ergibt dann das fertige Modell.
Prinzip:
Die bewegliche Basisplattform befindet sich in einer Prozesskammer, die flüssigem Kunststoff gefüllt ist. Für den Aufbau der ersten Schicht wird die Plattform bis knapp unter die Oberfläche gefahren. Ein Laser zeichnet die Konturen der ersten Schicht auf der Flüssigkeit nach. Durch die Lasereinwirkung härtet die Schicht an den gewünschten Stellen aus (Photopolymerisation). Die Plattform wird abgesenkt ein Schieber befördert neuen Kunststoff auf das Bauteil.
Werkstoffe: Epoxyharze und Acrylate
Vakuumgießanlage
Vakuumgiessanlage
HEK 4/01:
- Bauvolumen 450mm x 425mm x 500 mm
- max. Gießgewicht ca. 850 gr.
- SPS-Steuerung
- Material diverse Harze mit Eigenschaften von PP, PC, PA


Computertomographie

CT-Mini von Procon x-Ray:
- 130 kV Microfocus-Strahler
- Flat Panel Detektor 10 x 10 cm
- Auflösung bis zu 5 µm
- Messbereichserweiterung
- Auswertesoftware (3D-Darstellung, Porenanalyse, Stl-Generierung
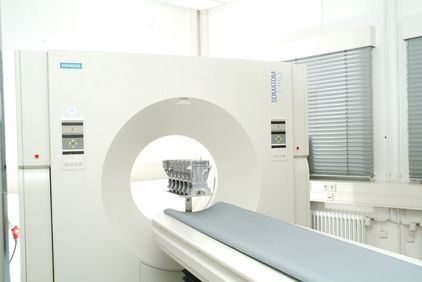
RS SOMATOM Plus 4 von Siemens:
- 500 ms Rotationzeit
- 160 Schichten in 20 Sekunden
- 100 Sekunden Spiraldauer
- 125ms zeitliche Auflösung
- min. Schichtdicke 0,8 mm



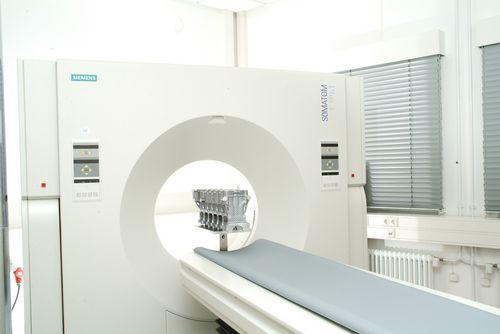
Kurze Entwicklungszeiten und Null-Fehler-Produktion erfordern Messverfahren, die zeit- und kostengünstig sowohl zerstörungsfreie Materialprüfung, eine Funktionsanalyse von gekapselten Baugruppen als auch dimensionelles Messen ermöglichen. Die industrielle 3-D-Röntgen-Computertomographie (CT) bietet hierzu eine gute Voraussetzung, denn mit ihrer Hilfe können in einer Messung sowohl Material- als auch Formfehler detektiert und spezifiziert werden.